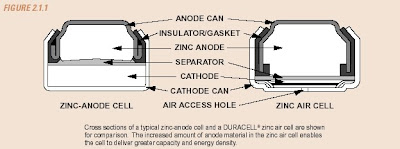
TECHNICAL BULLETIN
The sections of the Technical Bulletin may be downloaded as Adobe Acrobat PDF files for local viewing/printing.
You may download individual sections, or the entire document below.
Print this page Download PDF
Entire Zinc Air Bulletin
1. Introduction
The zinc-air primary battery system is different from most other batteries in that it “breathes” oxygen from the air for use as the cathode reactant. The virtually limitless supply of air enables the zinc air cell to offer many performance advantages compared to other batteries.
The electrochemical system can be more formally defined as zinc/potassium hydroxide/oxygen, but “zinc-air” is the common name and is used throughout this text. Other zinc anode battery systems are also referred to by their popular abbreviated names:
Zinc/alkaline/manganese dioxide -> Alkaline
Zinc/mercuric oxide -> Mercury
Zinc/silver oxide -> Silver
2. General Characteristics
2.1 System Description
The zinc-air battery was discovered in the early nineteenth century, but did not find its first commercial use until the 1930s when large industrial-type cells were constructed for railway signaling. The development of the thin and efficient air cathode used in today’s zinc-air cells occurred in the early 1970s. This led to miniaturization and ultimately to the commercialization of zinc-air button cells in 1977. The world of zinc-air today includes button cells, batteries, and a small number of customized battery packs. Zinc-air delivers the highest energy density of any commercially available battery system, and at a low operating cost. This advantage is derived from its use of atmospheric oxygen as the cathode reactant. It allows the zinc-air cell to be filled with more zinc "fuel", which is the only material consumed during discharge. This increased amount of anode material enables the cell to offer up to 5 times more capacity than conventional zinc anode systems which must contain their oxidant within the cell. For example, alkaline cells store oxygen in the form of manganese dioxide, which comprises about 60% of the cell weight. Most batteries contain roughly the same amount of anode material as cathode material, so their service life is limited by whichever is consumed first.
A schematic representation of a conventional zinc anode cell and a DURACELL® zinc air cell is shown in Figure 2.1.1. DURACELL® zinc-air batteries are used in a number of consumer and industrial applications. They are best suited for devices that are used frequently or continuously, operate at low-to-medium drain rates, and require high energy density and low operating cost. Hearing aids are an ideal application for zinc-air because they are usually worn for up to 16 hours per day and have a low-to-moderate requirement for electrical current (a few milliamperes on average). Zinc-air batteries are often used to power a number of medical devices, such as patient monitors and recorders, nerve and muscle stimulators, and drug infusion pumps. They are also well suited for use in telecommunication devices such as pagers and wireless headsets.
DURACELL® zinc-air cells can be combined in series and series-parallel connections to form a number of battery pack configurations. Such packs have been designed for use in communications equipment and emergency lighting products. To achieve optimum battery performance in the application of interest, Duracell may be contacted for assistance.
2.2 Advantages
The advantages of using DURACELL® zinc air cells are described below:
•High Energy Density – The zinc-air cell has a gravimetric energy density of up to 442 Watt-hours/kilogram (Wh/kg) (200 Watt-hours/pound) and a volumetric energy density of up to 1673 Watt-hours/liter (Wh/l) (27.4 Watt-hours/cubic inch). This is up to five times the energy of alkaline and mercury systems. The highest energy is delivered under conditions of frequent or continuous use, low-to-medium drain rates, and operating temperatures between 0 ºC and 50 ºC (32 ºF and 122 ºF).
•Flat Discharge Profile – Typically zinc-air cells maintain a constant output voltage between 1.1 and 1.25 volts throughout the discharge life of the cell.
•Excellent Sealed Shelf Life – The sealed (unactivated) zinc-air cell has been demonstrated to retain greater than 98% of its rated capacity after one year of storage at 21 ºC (70 ºF). The unactivated storage life is rated at 3 years.
•Intrinsically Safe – Zinc-air cells offer a means of self-venting any internally generated gases through air-access holes located on the cathode can, eliminating the possibility of cell rupture or explosion. In addition, zinc-air cells are generally considered environmentally safe, and under most conditions do not require special handling or disposal procedures.
•Low Operating Cost – Zinc-air cells and batteries offer a low operating cost on a per-milliampere-hour basis when used in frequent or continuous use applications.
2.3 Comparison of Primary Battery Systems
Primary batteries are most often described by their energy as a function of cell weight and volume. A per-unit-weight comparison of zinc-air with other primary systems is shown in Figure 2.3.1. The gravimetric energy density is greater than all other primary batteries over an operating temperature range of 0 ºC to 50 ºC (32 ºF to 122 ºF). The comparison on a volumetric basis is provided in Figure 2.3.2. Zinc-air to delivers its greatest energy per unit volume over a similar temperature range. Under some conditions not shown in the figure (50-100 mA/cm2), DURACELL® zinc-air cells can deliver up to five times the energy of other zinc-anode systems.
Figure 2.3.3 shows the discharge characteristics of conventional zinc-anode battery systems for cells of the same size over their discharge life at 21 ºC (70 ºF). Unlike alkaline cells, DURACELL zinc-air cells provide a constant output voltage during discharge.
During storage, zinc-air cells are sealed to prevent oxygen, the cathode reactant, from entering the cell. This characteristic gives the zinc-air cell excellent shelf life as shown in Figure 2.3.4. At 21 ºC (70 ºF) storage, a sealed zinc air cell retains 98% of rated capacity over a one-year period. Zinc-air cells are best if used within 3 years of manufacture.
3. Composition and Chemistry
3.1 Cell Chemistry
A DURACELL® zinc-air cell consists of a zinc anode, an aqueous alkaline electrolyte and an air cathode. Power is derived from the reduction of oxygen at the cathode, and the oxidation of zinc at the anode. The simplified net reaction is shown below:
Zn + ½O2 -> ZnO
3.2 Anode
The anode in a zinc air cell is a powdered zinc amalgam. The zinc powder contains a very low level of mercury (max. 25 mg per cell) to prevent internal pressure buildup due to hydrogen evolution from the self-discharge of the zinc in the electrolyte. A gelling agent is also mixed with the zinc amalgam to maintain the uniformity of the zinc powder-electrolyte mixture during discharge.
In the cell reaction, the zinc in the anode is oxidized to form zinc hydroxide in the form of the soluble zincate [Zn(OH)42-] ion. The half reaction for the anode is shown below:
Zn + 4OH- -> Zn(OH)42- + 2e-
The zinc hydroxide accumulates around the zinc particle, but does not impede either ionic or particle-to-particle conductance until the zinc is fully oxidized. As the discharge proceeds, the zincate ions eventually precipitate to form zinc oxide (ZnO).
Zn(OH)42- -> ZnO + H2O + 2OH-
Theoretical capacity of the anode is 0.82 ampere-hours per gram of zinc (23 ampere-hours per ounce of zinc).
3.3 Cathode
The air cathode in a zinc-air cell is a mixture of carbon, Teflon, and a small amount of manganese dioxide impressed onto a nickel-plated screen. This material is then laminated with a Teflon layer on one side and a separating membrane on the other. The Teflon layer allows gases, most importantly oxygen, to diffuse into and out of the cell, and also provides resistance to leakage. The separator acts as an ion conductor between the electrodes and as an insulator to prevent internal short-circuiting.
Atmospheric oxygen reacts with catalysts in the air electrode and electrolyte to produce hydroxide ions.
The half reaction for the air cathode is shown below:
½O2 + H2O + 2e- -> 2OH-
Theoretical capacity of the air electrode is 820 mAh/g, or 4.79 ampere-hours per liter (0.079 ampere-hours per cubic inch) of molecular oxygen, which is roughly equivalent to one ampere-hour per liter of air.
3.4 Electrolyte
The alkaline electrolyte employed in a zinc air cell is an aqueous solution of potassium hydroxide with a small amount of zinc oxide to prevent self-discharge of the anode. Potassium hydroxide provides good ionic conductance between the anode and cathode to permit efficient discharge of the cell.
4. Construction
4.1 Cell Construction
The button cell is a widely used battery configuration for hearing aids, calculators, infusion pumps, and pagers. The major components that make up a DURACELL® zinc-air cell are illustrated in Figure 4.1.1.
The anode subassembly includes the anode can and the insulator. The anode can, which holds the zinc anode, is a tri-clad material comprised of a copper interior lining for good chemical compatibility, a stainless steel layer in the middle for strength, and nickel layer on the outside for good electrical contact. A nylon insulator surrounds this can and insulates the negative terminal from the positive terminal. A sealant coating is applied to the insulator prior to its assembly with the anode can.
The cathode subassembly consists of the cathode can and the air electrode. The cathode can is made of nickel-plated steel, and contains multiple air holes punched into the bottom to provide air access to the cathode. These air holes provide the pathway for oxygen to enter the cell.
Placed directly over the holes is a porous membrane that helps ensure uniform air distribution across the air electrode. On top of this membrane is a loose layer of Teflon to help form the cathode seal, and then the air electrode itself (i.e. cathode), which is oriented with its Teflon side toward the air holes. There is an interference between the ends of the nickel screen that protrude from the perimeter of the cathode, and the cathode can to form a low resistance contact. The zinc-anode mix and the electrolyte are dispensed into the anode subassembly, over which the cathode subassembly is placed and sealed.
4.2 Tab Seal
Once constructed, the cells are sealed to provide a consistently fresh product to the end user. The seal comprises a special tab that is placed over the air holes and attached via a mild adhesive. DURACELL® zinc-air button cells are sealed with an EASYTAB, a tab that is longer than the tab on ordinary hearing aid batteries — making it easier to remove from the pack, handle and insert into the device.
4.3 Battery Construction
Battery cases are made of injection molded plastic with special porous inserts to allow air circulation around the cells. Some batteries may utilize a shrink-wrap plastic with air access ports. Cells are packaged to allow adequate and equal air access to each cell’s air access ports.
5. Performance Characteristics
5.1 Preparing Batteries for Use
Zinc-air cells are stored with an adhesive tab seal or, when in a battery, in a metallized plastic pouch that inhibits gas and vapor transfer. The batteries are ready to be used when the seal or pouch is removed, allowing oxygen from the air to enter the batteries. In most cases, nominal voltage levels are attained immediately after the seal is removed.
5.2 Voltage
The nominal open circuit voltage for a zinc air cell is 1.4 Volts. The operating voltage during discharge is dependent on the discharge load and the temperature. Typically, the operating voltage per cell is between 1.25 and 1.0 Volts. Zinc-air cells are noted for a relatively flat discharge profile, i.e. the voltage is relatively constant during use. The typical end point or cutoff voltage, by which most of the cell capacity has been expended, is 0.9 Volts.
5.3 Energy Density
Zinc-air batteries offer the highest gravimetric and volumetric energy density of any primary battery system, due to their use of atmospheric oxygen as the cathode reactant. The air electrode, the site at which the cathode reaction occurs, occupies very little internal volume and does not degrade throughout the discharge of the battery. The result is an increase in the volume available for the zinc anode (fuel), which translates into higher capacity.
To determine the energy density of a zinc air cell under specific conditions of load and temperature, simply multiply the capacity in ampere-hours that the cell delivers under those conditions by the average discharge voltage, and divide by the cell volume or weight. The equations for gravimetric and volumetric energy densities are shown below.
Gravimetric Energy Density:
(Drain in Amperes x Service Hours) x Average Discharge Voltage = Watt-Hours
Weight of Cell in Pounds or Kilograms lb. or kg
Volumetric Energy Density:
(Drain in Amperes x Service Hours) x Average Discharge Voltage = Watt-Hours
Volume of Cell in Cubic Inches or Liters in3 or L
CELL VOLUMETRIC ENERGY DENSITY GRAVIMETRIC ENERGY DENSITY
Watt-hours/liter
(Wh/L) Watt-hours/cubic inch
(Wh/in3) Watt-hours/kilogram
(Wh/kg) Watt-hours/pound
(Wh/lb.)
DA5 1,430 23 294 134
DA10 1,657 27 351 159
DA312 1,439 24 340 154
DA13 1,756 29 411 187
DA675 1,673 27 442 201
Table 1. Typical energy density of DURACELL® zinc-air button cells
As a general rule, energy density decreases as the cells get smaller since the percentage of inactive materials, such as insulators, current collectors and cell containers, consume proportionately more of the cell weight and volume. Table 1 lists the approximate energy density of various DURACELL® zinc air button cells.
5.4 Capacity
Zinc-air capacity is usually expressed in ampere-hours or milliampere-hours. The rated capacity of a particular cell is what is derived under the recommended specification for that cell. DURACELL® zinc-air cells are offered in a wide range of sizes and capacities. The capacity can be determined from the respective datasheet for each cell. As with all battery systems, performance of a zinc-air cell is dependent on the discharge current. As an example, capacity is plotted as a function of discharge current for various DURACELL® zinc-air cells in Figure 5.4.1. This graph provides an estimate of effective capacities and is to be used as a general guideline. For anticipated cell performance in a specific application, contact Duracell for information.
Cell performance can also depend on temperature and ambient relative humidity. Figure 5.4.2. shows how the delivered capacity of a DURACELL® zinc air cell is affected by the operating temperature.
5.5 Oxygen Starvation
Because of the unique design of the zinc-air battery and its use of air as the cathode, the zinc-air cell's performance is susceptible to the relative availability of air and must be considered when evaluating the capabilities of the zinc-air system. Technically speaking for all batteries, their performance begin to decline precipitously due to the finite speed at which the reactants and products can be delivered to and from the electrodes. In zinc-air, this is generally due to oxygen starvation. That is, as the current demand increases, the cell must provide air to the cathode at an increasing rate. When the rate of oxygen reduction is about equal to the replacement of air in the cell, the discharge current can be maintained without air starvation. At higher drain rates, the voltage begins to steeply decline. The reason that this parameter is so design dependent is that it is most typically correlated with the size and number of air holes. Zinc-air battery designers configure their cells to provide the just the right amount of air access for the applications in which the cells are used. Adding holes or making the holes larger increases the cell's rate capability, but it also decreases the activated life (see Section 5.9). DURACELL® zinc-air cells are optimized for maximum performance and life in the applications listed in this guide. Customers wishing to exploit the advantages of zinc-air cells in other applications should consult with Duracell to assess the product options.
5.6 Pulse Current Capability
The pulse current capability for a zinc-air battery can be many times greater than the maximum current that can be sustained under continuous discharge. Actual performance will depend on the pulse width and duty cycle. This relationship is illustrated in Figures 5.6.1. and 5.6.2., which show the pulse load performance of a typical zinc-air button cell. In Figure 5.6.1, a pulse current that is more than double the magnitude of the average current is applied, but the width and frequency are sufficiently low that that the cell does not become oxygen-starved before the end of a single pulse. The voltage profile exhibits the ripple effect of the pulse current, but the cell maintains a constant average operating voltage. In contrast, the cell in Figure 5.6.1 is subjected to an average load that is high relative to the pulse current. It suffers from oxygen starvation and exhibits a progressively declining load voltage.
5.7 Internal Impedance
Cell impedance is a critical consideration in some applications such as hearing aids where low impedance is required for proper operation. The internal impedance of zinc-air batteries is comparable to other zinc anode batteries of similar size. The internal impedance specification for each DURACELL® zinc-air battery (at 1000 Hz) is provided on the individual product datasheets.
--------------------------------------------------------------------------------
5.8 Shelf Life
Shelf life measures the ability of a sealed cell to retain capacity under specified storage conditions. Zinc air cells are essentially dormant until the cathode reactant, oxygen, is allowed to enter. Oxygen is excluded during storage by means of a low-porosity tab seal placed over the air holes. Removing this seal activates the cell by allowing oxygen to enter. As was shown in Figure 2.3.4., a sealed zinc-air cell stored at 21ºC (70ºF) will retain more than 98% of its rated capacity over a one-year period. The rated storage life is three years.
--------------------------------------------------------------------------------
5.9 Activated Life
Zinc-air activated life is a measure of the ability of the cell to retain its performance after the tab is removed (and not replaced). This differs from Service Life in that it refers to the undischarged condition. It is what happens to the battery when the tab is removed or the package is opened and it is placed on a shelf or counter top. Since zinc-air cells obtain the cathode reactant from the air, they are subject to the influence of the environment. More specifically, they can dry-out under conditions of low humidity, or become waterlogged at high humidity due to the ingress of water vapor. They also absorb oxygen and carbon dioxide from the air. The oxygen can dissolve in the electrolyte and react with the zinc. The carbon dioxide reacts with the electrolyte. Although the amount of carbon dioxide in the environment is small, its effects on the battery are cumulative.
It is possible to prolong the life of the battery by re-covering the air holes with the tab after each use, but the benefits of this strategy vary considerably and are highly dependent upon the environmental conditions. The best practice is to place the cell in the device and use it until it is discharged.
--------------------------------------------------------------------------------
5.10 Discharge Characteristics
In most applications, zinc-air cells provide a very stable output voltage throughout the life of the cell. The discharge characteristics of a typical zinc-air battery as a function of temperature are illustrated in Figure 5.10.1. The discharge rate is defined with respect to the cell capacity. For example, a 300-hour rate for a DA13 cell (nominal capacity ~ 290 mAh) would correspond to a discharge rate of approximately 0.95 mA (290 mAh/300 h).
Effect of Temperature
Optimum performance for zinc air batteries is achieved at temperatures between 0ºC and 50ºC (32ºF and 122ºF). At lower temperatures, a continually sloping voltage profile will be exhibited, with the degree of slope dependent upon on the temperature and the discharge rate. Performance at temperatures above this range may actually be improved in the short term, but long-term exposure to elevated temperatures can accelerate moisture loss, which can reduce performance.
Figures 5.10.2 and 5.10.3 show the effects of temperature at two additional rates of discharge. The curves illustrate that temperature becomes more significant parameter as the discharge rate increases.
Effect of Humidity
Relative humidity can affect the performance of a zinc air battery over long periods of use. Moisture transfer through the battery’s air access holes results from the difference in relative humidity between the interior of the cell and the environment. The effect of continued moisture loss or gain from the electrolyte would be seen as shortened life or loss of power. Best results over long-term discharge are achieved at relative humidity conditions between 35 and 80 percent.
Figure 5.10.4 shows an intermittent discharge (4 hours per day) of a DURACELL® zinc air battery at 30, 60 and 90 percent relative humidity conditions. Under conditions of 40-60% R.H., the outside world most closely matches the interior of the cell, at the maximum performance is obtained.
5.11 Cell Expansion
The discharge of a zinc-air cell results in a small increase in the overall cell volume as the zinc is oxidized. In the case of a DURACELL® DA675 cell, cell height increases by about five thousandths of an inch when fully discharged. If the battery is constrained so that it cannot expand, it may not realize its full capacity. In a multi-cell battery, the cells are packaged so that sufficient space is allowed for growth during discharge. All DURACELL® zinc-air cells are designed to fit within the IEC cell specifications during discharge.
6. Applications
6.1 Fundamentals of Battery Selection
To optimize battery performance, the battery selection process should begin in the early stages of equipment design before the battery cavity is fixed. In this way the most effective trade-off can be made between battery capabilities and equipment features.
In the battery selection process, the following fundamental requirements should be considered:
--------------------------------------------------------------------------------
--------------------------------------------------------------------------------
Voltage: Environmental Conditions:
Maximum permissible voltage, minimum operating voltage, startup time. Shock; vibration, humidity, other atmospheric conditions.
--------------------------------------------------------------------------------
--------------------------------------------------------------------------------
Load or Current Drain: Shelf Life:
Average current, constant power; variable load, pulse requirements. Capacity retention requirements, storage time, temperature.
--------------------------------------------------------------------------------
--------------------------------------------------------------------------------
Duty Cycle: Reliability:
Continuous or intermittent. Permissible variability, failure rates, potential for gassing or leakage.
--------------------------------------------------------------------------------
--------------------------------------------------------------------------------
Service Life: Safety:
Length of time operation. Type of usage (consumer, industrial, or military), abusive conditions.
--------------------------------------------------------------------------------
--------------------------------------------------------------------------------
Physical Properties: Contacts/terminals:
Size, shape, and weight. Compatibility with cell terminals, corrosion prevention.
--------------------------------------------------------------------------------
--------------------------------------------------------------------------------
Temperature: Cost:
Operating temperature range, storage temperature range. Operating or life cycle cost (i.e. cost per milliampere hour) and initial per-unit cost.
When the important fundamental requirements are identified, decisions can be made on the best battery system for the application. With so many types of batteries available today, choosing the best one can be a difficult task. There is no singular battery or battery system than best fulfills the needs of all applications.
If the application requires a low-cost, longer-life battery under a continuous or frequent use (many hearing aids used only on weekends) and/or a small battery package with high energy density, then DURACELL® zinc air batteries are an excellent choice.
6.2 Special Zinc-Air Design Considerations
The unique air-breathing property of zinc-air cells is the key to their high energy density and high capacity. This factor introduces application design considerations that do not pertain to conventional primary battery systems:
•Air Access
Air access is a critical aspect of designing equipment to use zinc air batteries. Air is admitted through the holes in the positive cap of each cell, so the holes must not be blocked. The oxidation of each atom of zinc requires a fixed amount of oxygen and provides four electrons to the external circuit. Based on this simple relationship, the amount of air required per ampere-hour of capacity is about 1.2 liters at standard temperature and pressure. It is difficult to provide hard and fast rules for designing proper air access, such as the size and number of holes or apertures, but simple calculations of gas transport via diffusion of air provide a good starting point. DURACELL ® zinc-air cells are designed to provide the most efficient air access for optimum power. Figure 6.2.1 provides an example of sample hole patterns for DURACELL ® and competitor cells.
•Contact Methods
The recommended locations for making electrical contact are the anode can top (-) and the cathode can side wall (+). If contact to the bottom of the cathode can is required, care should be taken to avoid the air holes and the "+" mark at the center of the can. An additional concern is the shape of the bottom of the battery which may either be flat or stepped, see Figure 6.2.2. The device manufacturer must correctly design their battery cavities to handle both battery shapes, since both bottom styles exist side-by-side in the marketplace. Improper design may result in poor fit of the cell within the device cavity. Table 2 provides some useful design criteria for use with DURACELL ® zinc-air cells.
•Device Voltage Cutoff
The nominal cutoff voltage for zinc-air cells is 0.9 Volts. They can be discharged to lower values, but deep discharge to 0.5 Volts or less can result in electrolyte leakage from the air holes. The recommended practice is to design the device with a voltage cutoff feature that shuts the equipment off at a predetermined voltage setting.
6.3 Zinc-Air Application Design Guidelines
The following design guidelines are provided to aid in identifying the types of applications that zinc-air batteries will best serve. They deliver their optimum service in devices that require:
•Highest capacity in a compact and lightweight form; (40 - 600 mah in single button cells, depending on size, and up to 1,500 mah in multicell batteries)
•Low to moderate drain rates (up to 20 mAh for the DA675) at an operating voltage of 1.25 to 0.9 Volts or a multiple thereof..
•Continuous or frequent use that fully discharges the battery within a two- to three-month period.
•Operation between 0°C and 50°C (32°F and 122°F).
•Long shelf life when in a sealed state awaiting use.
Application Examples
•Home Health Care Devices (e.g.. Crib Monitors)
•Hearing Aids (Behind-the-Ear and In-Canal Aids)
•Pagers
•Patient Monitors (Telemetry Transmitters)
•Portable Data Loggers
Figure 6.3.1 shows the discharge profile of a DURACELL ® zinc-air cell during a test typical of a conventional BTE hearing aid.
7. Handling and Disposal
The following care and handling procedures pertain to the various zinc-air cells manufactured by Duracell.
7.1 Safety
DURACELL® zinc-air cells are safe to use because they offer a means of self-venting any internally generated gases through the air access holes located on the cathode can. This eliminates the probability of cell rupture or explosion.
7.2 Packaging and Transportation
All DURACELL® zinc-air batteries are supplied in the sealed state in one of the following packaging styles:
•Two or more individual button cells sealed on one piece of adhesive tape
•Individual cells with their own tape seal (tab)
•Multicell batteries individually sealed in a metalized plastic pouch.
The factory seal should not be removed or the pouch opened until the battery is required for use. Generally DURACELL® zinc air batteries do not require special handling or shipping precautions for land, sea or air transportation.
7.3 Storage
As with any electrochemical system, ambient storage temperatures of 21°C (70°F) or cooler are recommended for best capacity retention. When storing zinc air batteries, do not stack more than three cases high, as the additional weight may cause damage to the internal cell packaging and potentially the cells.
7.4 Usage
Zinc-air cells should be used within the recommended operating conditions specified for each cell size. Optimum performance is obtained via operation on a frequent or continuous use basis within a temperature range of 0°C to 50°C (32°F and 122°F) and a relative humidity range of 25-80%. As is the case with all battery systems, zinc-air batteries should be removed from equipment that will not be used for prolonged periods of time.
When inserting zinc-air cells into equipment, attention must be paid to the polarity. Reverse insertion can cause charging and possible leakage. When a device requires more than one battery, all batteries should be replaced at the same time. Always use cells of the same chemical system to prevent voltage incompatibilities and potential leakage.
7.5 Disposal
DURACELL® zinc-air cells do not require special disposal or reclamation after being discharged
댓글 없음:
댓글 쓰기